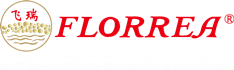
Solvents Extractants
SX-EW (solvent extraction and electrowinning) are distinct metallurgical unit operations that recover high purity metal from leachate solutions.Solvent extraction is used to concentrate materials in an organic solution, while electrowinning is used to recover these pay elements. The two procedures are often conducted together. While electrowinning can be used with other processes, it is always used after solvent extraction.
Florrea CoLIX® Solutions for Metal Solvent Extraction
Better Hydrometallurgy
SX-EW (solvent extraction and electrowinning) are distinct metallurgical unit operations that recover high purity metal from leachate solutions.
Solvent extraction is used to concentrate materials in an organic solution, while electrowinning is used to recover these pay elements.
The two procedures are often conducted together. While electrowinning can be used with other processes, it is always used after solvent extraction.
Many elements can be extracted from aqueous metal-rich leachate solutions and concentrated into an organic solvent. The pay elements are then removed from the organic solution by electrowinning. The resulting high purity metal plate is then directly sold.
Florrea CoLIX® Solutions offers a broad range of solvent extractants for purification and concentration of
ü Copper
ü rare earths
ü nickel/cobalt
ü lithium
ü molybdenum
ü zinc,cadmium
ü niobium
ü tanatalum
ü various other metals
Oxime-based range of copper extractants is used by copper producing mines in the world. This includes modified aldoximes, modified aldoxime: ketoxime blends, as well as specialized nitration-resistant and oxidation-resistant extractants.
Currently widely used copper solvent extraction reagents are Lix984N, Lix973NS-LV , Lix63, Lix84-A, Lix84-ICNS, Acorga M5760 and M5774 etc
Florrea copper extractants CoLIX® 1098 , CoLIX® 1033, CoLIX® 1037 are also working and servicing the copper mining industry as well as BASF Lix reagents hydroxoximes-cheating agents and Acorga extractants.
The acid-based range of extractants is used in a wide variety of metal applications such as:
ü Separation of cobalt from nickel
ü Separation of cobalt and nickel from manganese and magnesium
ü Extraction of molybdenum
ü Extraction of lithium
ü Recovery of rare earth elements
Florrea CoDiluent ® series are used as diluents for the solvent extraction of minerals including copper, nickel, cobalt, uranium and zinc.
Diluents available currently in world wide application is Escaid™ 110, Escaid™ 115 and Escaid™ 120.
Florrea CoDiluents are High-performance diluents for metal extraction and functions similar to Escaid.
Florrea CoDiluent ® 180 , CoDiluent ® 190 diluents are proved good in metal extraction.
They provide higher flash point, lower vapor pressure and much lower aromatic content to the mining industry compared to traditional kerosene extraction diluents.
Cytec’s CYANEX solvent extraction reagents are derivatives of organophosphines.
Phosphinic and thiophosphinic acids form complexes with metal cations, whereas phosphine oxides and sulfides are solvating agents.
CYANEX 272, CYANEX 301, CYANEX 921 and CYANEX 923 extractants have a high extraction coefficient for many metals. Extraction occurs at a low pH where cobalt and nickel can be co-extracted and calcium, magnesium and manganese effectively rejected.
They are for the most common commercial applications – primarily cobalt/nickel separation
Florrea CoLix ® 7605,7607,7607 and 7607A solvent extraction reagents function similar as CYANEX.
Alamine range of solvent extractants like Alamine 300, Alamine 304-1, Alamine 308,Alamine 330, Alamine 336, Aliquat 336 TG, Adogen381 are also most common solvent extractant to be used .
Florrea CoLix ® 7600,7601,7602 and 7603 solvent extraction reagents function similar as Alamine, Adogen and Hostarex .
Florrea offers a range of processing aids to promote organic phase quality, improve efficiency of clay treatment or optimize electrowinning operations.
Florrea work with local partner team to provide customers a complete package - reagents, application support, technical service and modelling capabilities - to help mining operations improve their productivity and reduce operating costs while meeting complex economic, environmental and metallurgical challenges.
Solvent extraction is a process in which compounds are separated based on their relative solubilities.
This treatment method involves using a solvent - a fluid that has the ability to dissolve another substance.
Solvent extraction is used across multiple industries, including during the processing of perfumes and vegetable oil. It’s also commonly used in petrochemical refining industries.
Solvent extraction is used to separate hazardous contaminants from sludge and sediments as well. This can be especially beneficial for hazardous waste generators since solvent extraction ultimately reduces the amount of hazardous waste that must be treated.
Solvent extraction does not destroy a compound. It instead separates it, a process that can provide several valuable benefits depending on the industry in which the process is used.
First Step: Extraction
Fundamentally, solvent extraction (S-X) starts with a mass transfer operation in which a constituent of one solution is transferred to another solution through an interface between the two. Since we are concerned here only with application to extractive metallurgy, the first solution is always a water solution of the desired element and the second is the organic solvent.
This first step in the process is called the extraction. It is governed by the laws of chemistry applicable to the reactions involved and by the practical aspects of mixing two immiscible liquids in such a way as to make the transfer of the desired constituent feasible from both the technical and economic standpoints.
Second Step: Stripping
The second major part of the S-X operation is the recovery of the desired material from the organic solvent in a purified and concentrated form in such a way that the organic solvent can be recycled to the extraction operation. This second step is usually called “stripping.”
In general, the extraction step does the largest degree of purification because of the selectivity of the solvent used while the major part of the concentrating is done during stripping.
Regardless of how complex a circuit may be with wash steps, reflux, regeneration and so forth, the two basic parts: extraction and stripping, can always be identified.
Choice of Solvent
In order to be used profitably the organic material which serves as the extractant must have a variety of properties. Of prime importance is the specific reactivity of the solvent with the particular element desired. Some properties are the same for all solvents, i.e. stability, low toxicity, high flash point; others are strictly dependent upon the particular element and solution involved. In fact, the complexity and multiplicity of choices facing the extractive metallurgist are almost bewildering and sometimes it is difficult to know how to start the development work. Here the basic chemistry of solvent extraction must serve as a guide.
There are two types of solvent extraction processes which must be considered. The first of these is sometimes called liquid ion exchange because of its similarity chemically to the ion exchange resin type of extraction which is well known to the extractive metallurgy industry. In this kind of extraction a small quantity of an organic chemical is dissolved in a second organic liquid called the diluent. This diluent may be a material such as kerosene or some other inert hydrocarbon, but its essential function is to serve as a carrier for the active solvent component. During the extraction operation the active component reacts chemically with the desired ions in the aqueous feed forming a new compound which is soluble in the inert diluent, or carrier.
Solvent Extraction Equipment
In principle any system which achieves mixing and separation of phases, can be used for solvent extraction in hydrometallurgy.
As a practical matter, however, the extractive metallurgy industry has pretty widely adopted the mixer-settler concept. There are a number of reasons for this, one of them is that the mixer-settler device is more amenable to handling slight amounts of solids which sometimes occur in operating mill solutions.
Another reason for adoption of mixer-settlers is that they involve less capital cost and are very simple to operate and have a high degree of operating leeway without fear of flooding. With proper design all flows can be observed by the operator and sampled as required. They can also be started up or shut down without any particular control problem.
The evolution of the mixer-settler systems for hydrometallurgical applications has gone through various phases. In some of the early applications both the organic and aqueous phases were pumped from stage to stage. Recycling where required was handled by airlifts or pumps. In a later development the aqueous or the organic phase flowed by gravity while the other phase and recycle was pumped. The latest evolution is the arrangement where the impeller in the mixer is of such design that it pumps both phases including organic or aqueous recycle if required. A diagram of how this is done in practice is shown in Figure 6. A photograph of an actual installation using this principle is shown in Figure 7.
With the development of new solvents, adequate laboratory techniques for working out new flowsheets, and the availability of practical commercial size equipment a bright future can be predicted for the use of solvent extraction in extractive metallurgy.
Conventional Copper Extraction
Conventionally, copper is recovered by a pyrometallurgical process known as smelting. In this process copper ore is mined, crushed, ground, concentrated, smelted and refined. The mining, crushing and grinding portions of the processing are extremely energy intensive since the rock must be reduced essentially to talcum powder fineness in order to separate the copper-bearing minerals from it. To be applicable to this process, the ores must contain copper minerals in sulfide form; as mineral such as Chalcocite (Cu 2S), Chalcopyrite (CuFeS 2) and Covellite (CuS) . In the concentrating operations these minerals are separated from the gangue material of the ore, that might contain as little as 0.5% copper to form a concentrate containing 27 to 36% copper. In the smelting operation, the concentrate is fed to a smelter together with oxygen and the copper and iron sulfides are oxidized at high temperature resulting in impure molten metallic copper (97 to 99%), molten iron oxide and gaseous sulfur dioxide. The impure copper is then purified by electrolytic purification to 99.99% pure copper while the iron oxide is disposed of as slag.
Typically, in this process there is more sulfur dioxide produced by weight than there is copper. Rather than discharge the sulfur dioxide into the air, as was once the practice, the sulfur dioxide is captured and converted into sulfuric acid. In the United States, smelter-produced sulfuric acid amounts to approximately 10% of total acid production from all sources. Prior to the mid-1980s, this by-product sulfuric acid had to be sold to other industries, often at a loss due to the long shipping distances.
Beginning in the mid 1980s a new technology, commonly known as the leach-solvent extraction-electrowinning process or, SX/EW Process, was widely adopted. This new copper technology utilizes smelter acid to produce copper from oxidized ores and mine wastes. Today, worldwide, approximately 20% of all copper produced is produced by this is process. In Latin America, the total is closer to 40% whereas in the United States the total is approaching 30%.
The SX/EW process has provided the copper industry with a tool that makes the extraction of copper from its ores significantly more environmentally friendly than by the use of the conventional smelting process. While the SX/EW process was adopted by the industry to take benefit from the sulfuric acid that the smelting process produced steps are being take to divorce the two.
The SX/EW Process
The SX/EW Process is a hydrometallurgical process since it operates at ambient temperatures and the copper is in either an aqueous environment or an organic environment during its processing until it is reduced to the metal. Because of its dependence on sulfuric acid, the SX/EW Process is at present not a substitute for, but rather an adjunct to conventional smelting. However, it is also applicable in locations where smelter acid is not available by the purchase of sulfuric acid or the manufacture of sulfuric acid from sulfur or pyrite. In addition, it offers the opportunity to recover copper from an entirely different set of ores and mining byproducts than is possible by smelting; namely, oxidized materials.
These may be mined copper minerals that are in oxidized form - minerals such as
Azurite (2CuCO 3 · Cu(OH)3), Brochantite (CuSO 4), Chrysocolla (CuSiO 3 · 2H 2O) and Cuprite (Cu2O), residual copper in old mine waste dumps whose sulfide minerals have been oxidized by exposure to the air or sulfididic copper minerals that have been oxidized by another new technology - bacterial leaching. In addition, the process can be used to extract copper in situ.
That is, without removing the material from the waste pile or from the ground. The net result of the use of this process is that copper can be produced from sources that in the past would have gone untouched, thus reducing the reliance on conventional ore bodies. Further, the process is capable of removing copper from waste materials where otherwise it would have been considered a contaminant to the environment. In the United States, for example, copper is considered to be a toxic material released to the environment once it is mined under Emergency Planning and Community Right-to-Know Act (EPCRA) and the Environmental Protection Agency's Toxic Release Inventory (TRI). Copper mine dumps and flotation tailings constitute a significant inventory of copper that is considered to be a contaminant to the environment under TRI.
The SX/EW process, itself, has very little environmental impact because its liquid streams are very easily contained, There is no effluent inasmuch as all impurities are returned to the site where they originated and the sulfuric acid is eventually neutralized by the limestone in the ore body or waste dump where it is deposited as calcium sulfate (gypsum) - a very insoluble substance.
The SX/EW Process has its roots in analytical chemistry where it is used to separate one metallic ion from another
The key to the process is the development of organic extractants that are specific to the metal to be extracted. The first extractant that was specific for copper and used on a commercial scale was developed by General Mills Corporation and sold under the name LIX 64® .
The process involves leaching the material with a weak acid solution. This solution, known as pregnant liquor, is recovered and then contacted with an organic solvent, referred to as the extractant, in the solvent extraction stage (SX). Here the copper is extracted away from the aqueous phase leaving behind most of the impurities that were in the leach solution. Since the copper ion is exchanged for hydrogen ion, the aqueous phase is returned to its original acidity and recycled to the leaching step of the process. Meanwhile, the copper-bearing organic phase is stripped of its copper by contacting it with a strongly acidified aqueous solution at which time the copper is moved to the aqueous phase while the organic phase is reconstituted in its hydrogen form. The copper-bearing aqueous phase is advanced to the electrowinning (EW) stage of the process while the barren organic phase is returned to the extraction stage of the process. In the electrowinning stage of the process the copper is reduced electrochemically from copper sulfate in solution to a metallic copper cathode. Electrowon copper cathodes are as pure as or purer than electrorefined cathodes from the smelting process. Thus they are well received by the market.
Another advantage of the process is its low capital investment requirement relative to the smelting process and its ability to be operated economically in a small scale. In China, for example, where copper deposits are not plentiful and tend to be small, there are 40 to 50 "mom & pop" leaching operations involving SX/EW.

Better mining reagents and solutions.innovative flotation reagents.
Creating Value for Environment, Society & Business
Related News
Tailings Management
Florrea partners with mineral processing companies to engineer tailings dewatering solutions that recover as much water as possible, giving you a more sustainable tailings disposal process while extending the life of your tailings storage facility and try to increase as much as possible the amount of a traditional tailings disposal solution – which ultimately helps to defer the heavy cost of building a new facility.
Zim container ship burns off coast of Canada
Zim container ship burns off coast of Canada
Florrea Dispersants
Florrea Dispersants